Aluminum processing
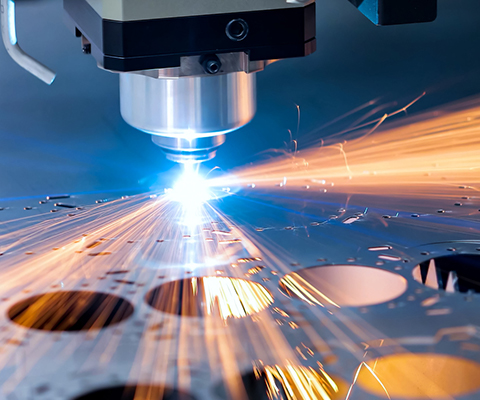
Yongyi provides aluminum material processing services. Its processing materials include S50C, SCM440, SKD61, SKD11, SK3, SS41, etc. The completed steel processing parts can be widely used in many industries, including the optical industry and automation equipment industry…etc. We also provide customized design assistance and related services. Please refer to the samples below. If you need detailed product information, please feel free to contact us at any time.
In the field of CNC machining, aluminum material processing is a very common and widely used process because aluminum is lightweight, high-strength, easy to process and has good electrical conductivity, and is widely used in aerospace, automotive, electronics and machinery industries. The processing of aluminum is relatively simple, but you still need to pay attention to its characteristics, such as easy scratching, thermal expansion, etc. The following is the detailed engineering process flow for aluminum material processing:
- Design and preparation
Product design: According to customer needs, use CAD software to design aluminum parts and determine their structure, size and surface requirements. The workability of aluminum needs to be considered when designing to avoid complex or unnecessary designs.
Material selection: Aluminum is available in many alloys, such as 6061, 7075, 5083, etc. Each aluminum alloy has different strength, corrosion resistance and workability. Choose the appropriate aluminum material according to product requirements.
Tool selection: For aluminum processing, carbide tools, steel tools or CNC tools are generally selected. The shape and material of the tool should be selected according to the processing requirements. - CNC program settings
CAM programming: Use CAM software to generate CNC machining programs (G code) to determine the tool’s motion path, cutting speed, feed rate, etc. The cutting process of aluminum material is relatively simple, but the cutting parameters need to be adjusted according to the properties of the aluminum material to maintain processing accuracy and surface quality.
Process path planning: Determine the appropriate processing sequence and reasonably arrange the processes of rough machining, semi-finishing and finishing to reduce stress concentration and deformation, and improve processing efficiency. - Preparation for processing
Clamping and positioning: Firmly fix the aluminum material to the table of the CNC machine. Aluminum is soft and easily deforms, so a suitable clamp is required to secure and prevent the workpiece from slipping.
Check equipment: Check the status of CNC machine tools and cutting tools to ensure equipment accuracy and avoid tool wear or machine tool abnormalities affecting processing results. - CNC machining process
Rough machining: Rough machining is performed to remove most of the material and the shape is roughly completed. The feed rate for rough machining is larger, but the cutting depth and cutting speed need to be controlled to avoid overheating or deformation of the material.
Semi-finishing: Semi-finishing is performed after roughing to get closer to the final size and prepare it for finishing. At this stage, attention should be paid to controlling the cutting force to avoid deformation of the aluminum parts.
Finishing: Finishing using small tools to ensure the part reaches its final dimensions and surface finish. When finishing, choose lower feed speeds and cutting speeds to ensure that the surface is scratch-free and meets high-precision requirements.
Cooling control: During the aluminum processing process, cutting fluid is required to cool the tool and reduce friction, so as to avoid oxidation of the aluminum surface or tool damage caused by high temperature. Proper cooling can improve machining accuracy and extend tool life. - Quality inspection
Dimensional inspection: Use tools such as vernier calipers, micrometers, and three-dimensional coordinate measuring instruments to check the dimensional accuracy of aluminum parts to ensure that they meet the design requirements.
Surface inspection: Check the aluminum surface for scratches, oxide layers or other defects to ensure that its appearance meets standards.
Functional testing: According to customer requirements, perform mechanical, hardness, corrosion resistance and other performance tests to confirm that aluminum parts achieve the expected performance. - Post-processing
Deburring: Aluminum is prone to burrs during processing, so deburring is required. This can be done by mechanical methods (such as sanding) or hand sanding.
Surface treatment: Surface treatment is performed on aluminum parts according to requirements, such as anodizing, sandblasting, polishing, etc. Anodizing not only improves the appearance of aluminum, it also improves its corrosion and wear resistance. - Packaging and shipping
Packaging Protection: Aluminum is relatively lightweight and scratches easily, so it needs good packaging treatment. Packaging materials usually include foam, sponge, plastic film, etc. to avoid damage during transportation.
Shipment and delivery: Send the processed aluminum parts to customers and provide necessary technical support and after-sales service.
Things to note
Heat treatment issues: The thermal expansion coefficient of aluminum materials is large. Excessive cutting temperatures need to be avoided during processing to prevent deformation or surface oxidation of aluminum materials.
Cutting parameter adjustment: According to the type and hardness of the aluminum alloy, adjust the cutting parameters to achieve the best processing effect. Softer aluminum alloys require higher cutting speeds, while harder alloys require lower speeds.
Tool selection: Aluminum has a soft surface, so the tool you choose needs to have good wear resistance. Using higher quality tools can improve machining accuracy and extend tool life.
Surface finish: The surface of aluminum after processing requires special attention because the surface is easily scratched or has an oxide layer. Post-treatment, such as anodizing, can improve the surface and prevent corrosion.
summary
The CNC machining process for aluminum is relatively standard, focusing on selecting the appropriate material, tool, and cutting parameters, as well as taking care to control cooling and surface preparation. Through precise processing, various precision aluminum parts can be manufactured to meet the needs of various industries, such as automobiles, aviation, electronic products and other fields.
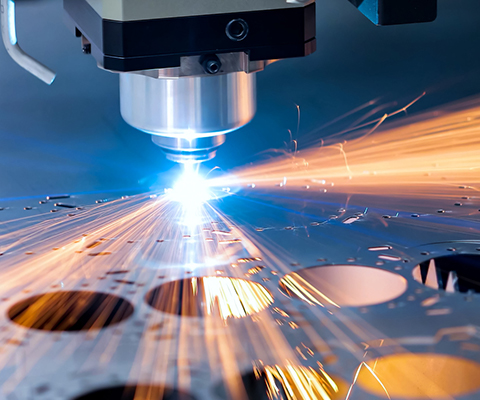
Yongyi provides aluminum material processing services. Its processing materials include S50C, SCM440, SKD61, SKD11, SK3, SS41, etc. The completed steel processing parts can be widely used in many industries, including the optical industry and automation equipment industry…etc. We also provide customized design assistance and related services. Please refer to the samples below. If you need detailed product information, please feel free to contact us at any time.